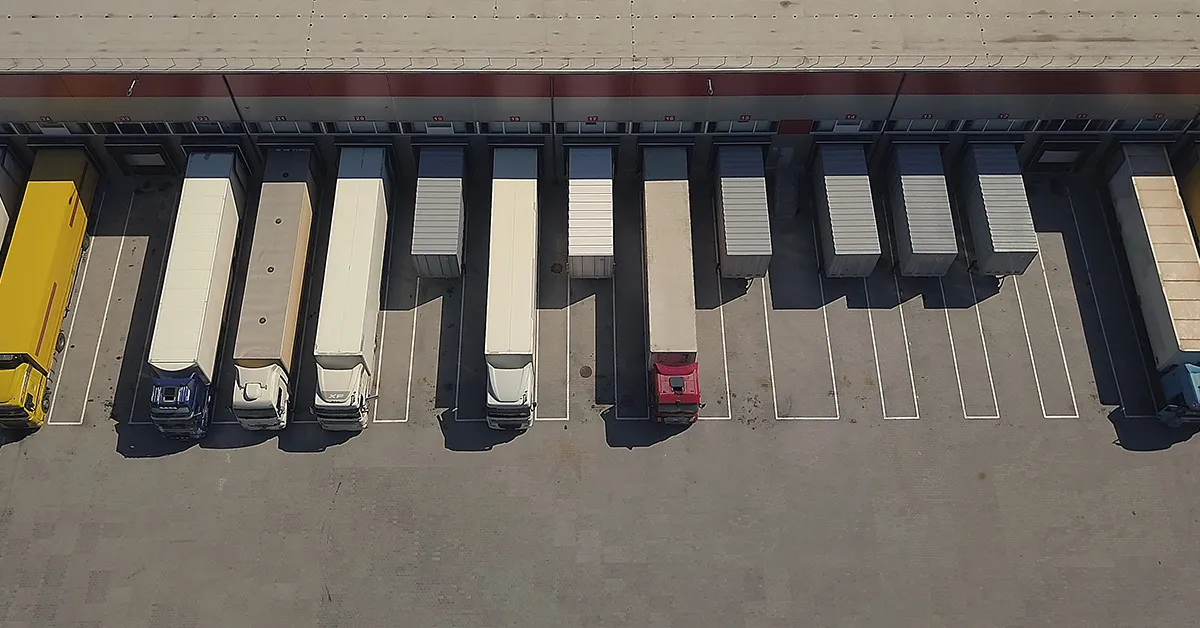
Since March 2020, the warehousing and logistics industry has faced some of the most significant supply chain shocks in decades. The combination of rolling shutdowns in manufacturing, a shortage of inventory and the nearly predictable oversupply that followed shed a glaring spotlight on the importance of smart warehousing practices.
The industry faces a promising outlook in the years ahead, but that doesn’t mean things will look the same. Find out where we are and what’s next for the warehousing industry.
Market and Industry Trends for Warehousing
As the world passes the third year of COVID-19, it’s important to remember that pandemic-related factory closures persisted in parts of the world through most of 2022. Widespread closures in China posed considerable production delays in Q4 that stretched into the new year, sidelining millions of workers.
The persistent and often unpredictable nature of these shutdowns reflects the uncertainty facing companies worldwide as they prepare, adapt, adjust and pivot again.
At first blush, the warehousing industry remains healthy. The market is valued at $263.4 billion in 2021 and is expected to maintain a 7.23% CAGR through 2027. That growth rate could undershoot the market as demand continues to outstrip supply. In the US, industrial warehouse capacity is around 1% in most competitive markets. Emerging markets warehousing is also shrinking, currently at less than 4%.
Learn more about our Supply Chain and Logistics Services
Building to Meet Warehousing Demand
Warehousing, storage and logistics will remain tight for the rest of the decade. Despite headlines touting canceled projects, 400 million square feet of warehousing are in the pipeline, with almost all of it leased. Industry experts predict another 400 million square feet will be needed by Q1 2023 to meet the growth forecasts.
Developers are rushing to turn existing facilities into short- and long-term warehouses. From shuttered shopping malls and big box stores to empty office buildings, there’s a concerted effort to meet demand in a matter of months, not years.
Warehousing and Distribution Outlook: What’s Next?
The future of warehousing and logistics will address the square footage problem and other inefficiencies that cost companies billions. Retail, industrial and manufacturing customers may rely on different material inputs but often share common warehouse problems and barriers.
Problem: Labor shortages
A robust labor market has made recruiting even more challenging in the warehousing industry. There’s been a disconnect between the remote logistics teams and on-the-ground labor. Just as thousands of technology experts receive layoff notifications, most warehouse operators can’t hire the help they need.
Solution: Automation
Still discussed in the media as a futuristic development, robotics are operating at warehousing storage facilities at hundreds of locations. Robots today serve several functions in improving warehouse efficiency through specialized designs, including:
- Robot pickers – Also known as pick-and-place robot arms, these programmable devices can select and move up to 300 items per hour to accomplish packaging, sorting and assembly tasks.
- Automated Guided Vehicles – Well before self-driving cars hit the highway, AGVs are used to move materials and goods across the often vast distances of a storage facility.
- Automated storage and retrieval systems – An ASRS can place and locate raw materials and products quickly and easily. They also increase warehouse safety by moving objects on high shelves, increasing retrieval speed and reducing the need to put humans in forklifts.
Automation is one component of lean warehousing. Lean warehousing is a management style that prioritizes efficiency by simplifying operations, forecasting and avoiding overstock inventory, and using several automation techniques.
Problem: Labeling, Tracking and Accounting
Poor labeling and accounting practices lead to costly delays and inaccurate shipments. This is especially important for raw materials and ingredients with expiration concerns. Implementing advanced labeling and tracking reduces inefficiency by increasing picking accuracy and providing real-time data to warehousing logistics teams and their customers.
Solution: Invest in Warehousing and Inventory Management Services
Working with third- and fourth-party warehousing service providers gives businesses the flexibility during volatile demand periods without overextending themselves with long-term costly leases. Tapping into these resources also helps to achieve geographic diversification by leveraging global warehousing, distribution and formulation services close to satellite production facilities.
Problem: Overstock Inventory
On the heels of supply chain shortages came a glut of inventory overages that pushed warehousing capacity to its limits. While retailers have been hit especially hard, many verticals have struggled to move excess products as supply chains got up to speed and market demand eased.
Solution: On-demand Warehousing
As additional warehousing comes online, look for short-term leases to provide on-demand, seasonal or low-commitment options for accommodating high inventory levels on an as-needed basis. Many businesses are also looking to incorporate third-party storage as a permanent part of their warehousing mix. Partners like Tilley Distribution provide the flexibility required to absorb overstock and move products where demand is on the rise.
Distribution Services Done Differently
For every warehousing problem, there are often several solutions that address immediate, short-term and long-term priorities. With more than 30 warehousing and storage facilities across the globe, proprietary truck and rail capabilities and a proven team of logistics experts, Tilley Distribution is here to provide the right solutions to support your goals. Let’s get started; speak with a Tilley representative today.